Vacuum valve design plays an important role in the functioning of a vacuum system. Many factors need to be weighed when choosing the type of valve(s), such as:
- Pressure range
- Type of application
- Expected service life
- Price
- Ease of maintenance
- Strength of seal required
Ball valves, angle valves, and gate valves all possess their own strengths and weaknesses when it comes to these different factors; this guide is here to go through each one.
Vacuum Ball Valves
Advantages
The design of a vacuum ball valve is very simple: it is a rotatable ball with a hole running through it. Ball valves possess six big advantages, which are:
- Ease of control/actuation
- Use in “dirty” vacuum applications
- Self-cleaning action around ball
- Different configurations/sizes
- High Vacuum Suitable
- XL Design prevents stem leak
A ball valve can be quickly rotated in a quarterly manner to be completely open or completely closed. Ball valves are much quicker to open and close than gate valves and poppet valves, which can be important in certain cases.
Ball valves are ideal for “dirty” vacuum applications, such as Metal-Organic Chemical Vapour Deposition, since they have less sensitivity to particulate contamination than other vacuum valves. This low sensitivity is also the reason that ball valves are commonly used to isolate scrubbers and traps downstream of the rough pumping system.
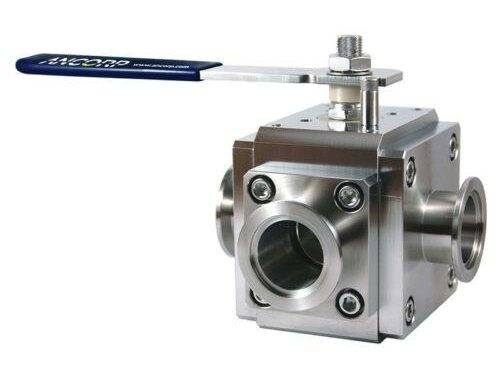
The design of a vacuum ball valve is very simple: it is a rotatable ball with an opening that runs straight through. Ball valves possess six major advantages, which are:
- Ease of control/actuation
- Use in “dirty” vacuum applications
- Self-cleaning action around ball
- Different configurations/sizes
- High Vacuum Suitable
- XL Design prevents stem leak
Vacuum ball valves can be quickly rotated in a quarterly manner to be completely open or completely closed. Ball valves allow faster opening and closing than gate valves and poppet valves, which can be important in certain applications.
Vacuum ball valves are ideal for “dirty” vacuum applications, such as MOCVD, PVD, CVD, and other thin-film coating processes, since they have less sensitivity to particulate contamination than other vacuum valves. This low sensitivity is also the reason that they are commonly used to isolate scrubbers and traps downstream of the rough pumping system.
Another benefit to vacuum ball valves is that the design features a self-cleaning action provided by the Teflon seats that wipe the ball clean as it’s opened and closed. This self-cleaning action prevents buildup around the ball and allows the valve to hold up extremely well in particle-rich effluent streams.
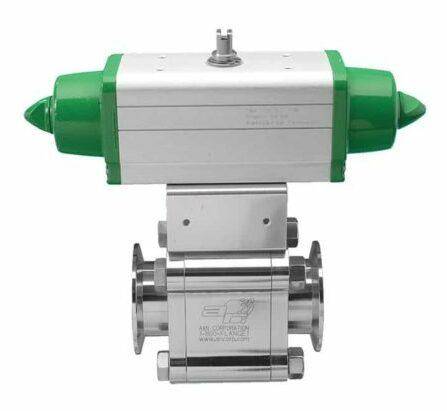
Vacuum ball valves also come in many different configurations and sizes, such as two-way, three-way, and high conductance. This provides great flexibility depending on the requirements of the user’s system. These different designs feature easily available replacement parts such as seats and seals.
Along with the other two types of vacuum valves, ball valves are suitable for high vacuum systems, with a pressure range of 10-8 Torr to atmosphere. A FKM seal can be used for ball valves at high vacuum conditions.
As discussed in the disadvantages below, ball valves are generally prone to leaks and improper stem assembly. ANCORP’s patented XL stem design helps avoids leaks and greatly reduces the risk of improper stem assembly.
Disadvantages
Ball valves generally include a few disadvantages, including:
- Stem complications
- Size limitations
Due to the design of many ball valves, issues such as stem leaks and valve seat leaks have been known to happen. These leaks can be costly and can negatively affect the entire vacuum system. Ball valve stems are also prone to improper assembly during the initial install and during maintenance. Because the poppet and gate valves do not have stems, those valves avoid this risk completely.
Ball valves are also at a disadvantage in terms of size. Gate valves can be much larger in size because of their design, thus can be used for applications that require a large valve. Ball valves are limited to applications that only require smaller valves.
As discussed, the risk of stem complications happening can be greatly reduced using ANCORP’s ball valve with the XL stem design. The design itself ensures that leaks are greatly limited, and the simplicity makes assembly much easier.
Overall
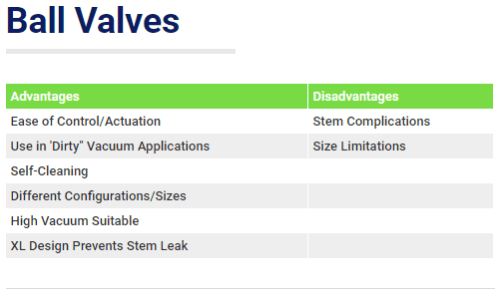
Vacuum Angle Valves
Advantages
The vacuum angle valve design features 3 main parts:
- Actuator
- Body
- Internal poppet
The actuator, which comes in a manual and pneumatic version, transports the poppet linearly in the body. When the poppet is positioned in the top section of the valve, the cavity is open to the system and flow is unimpeded. When the poppet is positioned in the bottom section of the valve, an elastomer sealing ring creates a vacuum tight seal by compressing between the poppet and sealing surface.
Vacuum angle valves come with several advantages, including:
- Different configurations
- Reliability in diverse applications
- Material Strength
- Ultra-high vacuum (UHV) and Extreme High Vacuum (XHV) suitable
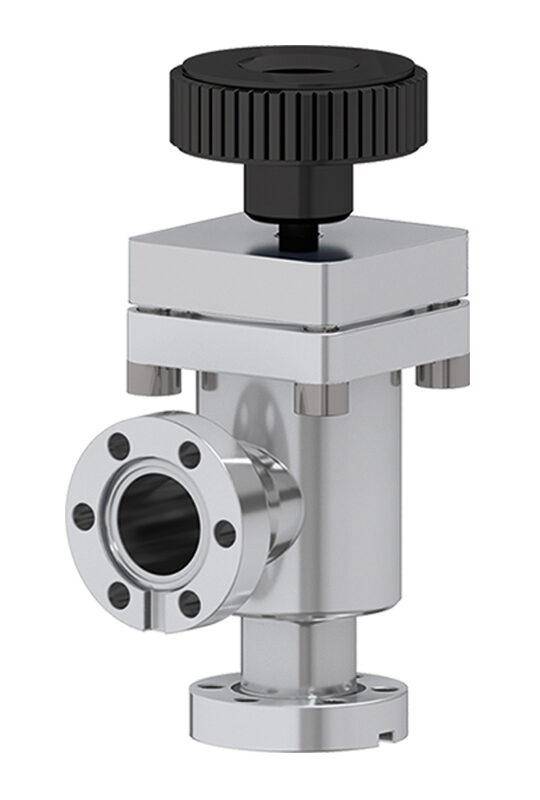
A major benefit to angle valves is that they come in diverse configurations, which allows them to be positioned into several different vacuum system layouts. Some of the configurations include angle, offset in-line, and in-line. Those three configurations are illustrated below:
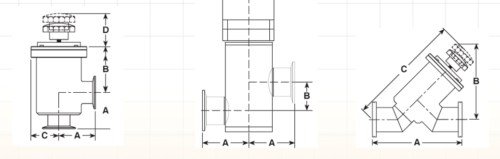
Vacuum angle valves also function reliably in a diverse array of applications. These applications range from semiconductor manufacturing, high-energy physics research, and even nuclear accelerators. The fact that poppet valves can hold up in the most extreme applications gives many users peace of mind in trusting them in their vacuum systems.
ANCORP is a distributor of VAT poppet valves, which feature bodies made of aluminum and stainless steel to promote strength and longevity. These materials ensure corrosion resistance and high purity in the body.
Disadvantages
Vacuum angle valves have one major disadvantage:
- Susceptibility to byproduct damage and buildup
Angle valves are susceptible to damage from byproducts traveling through the vacuum system. The bellows in the valve are susceptible to etching and cracking since they sometimes are exposed when opening or closing the seal. Ball valves and gate valves avoid this issue since they do not contain bellows. The sealing surface itself can also accumulate byproducts over time, which can be costly. This issue can also be avoided by using a ball valve.
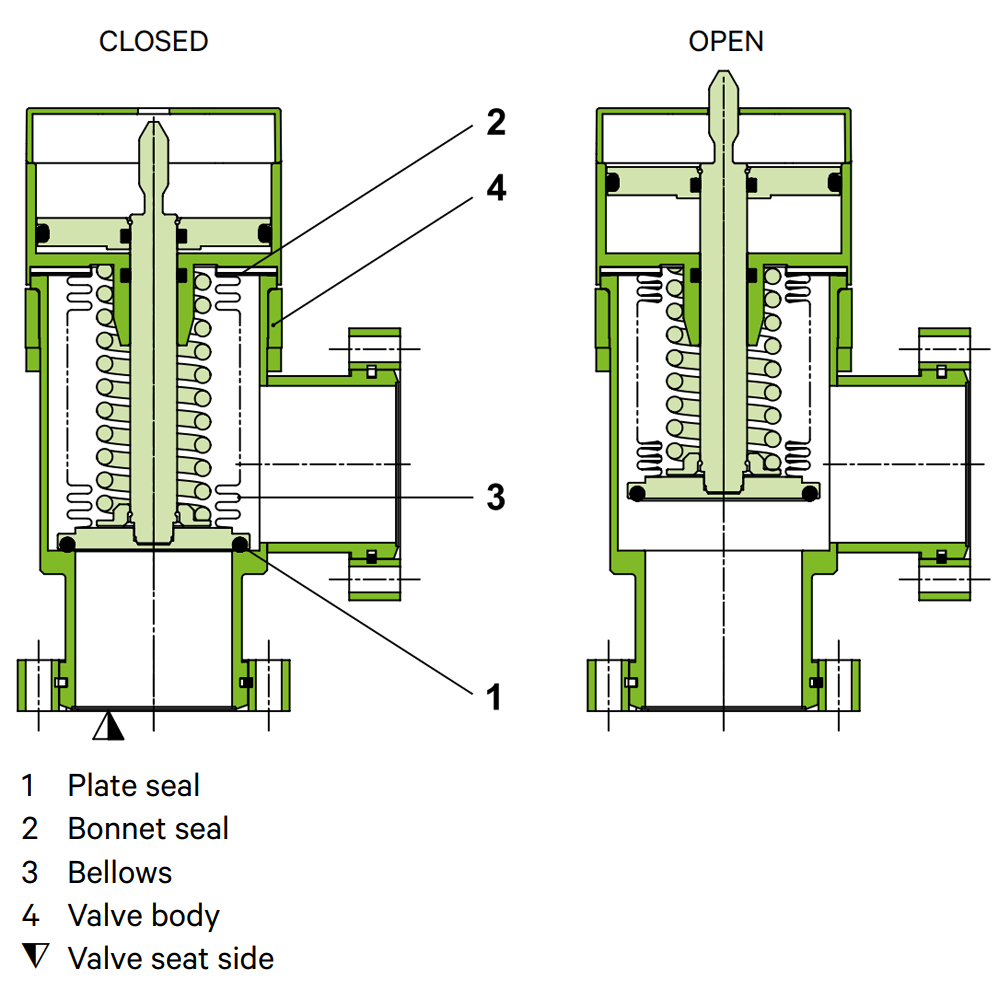
Overall
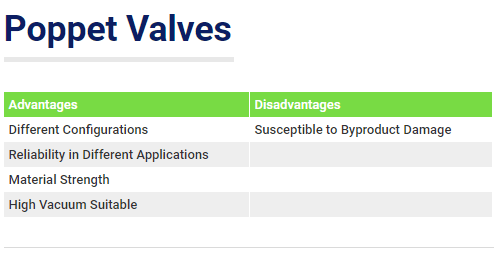
Vacuum Gate Valves
Advantages
The vacuum gate valve design features 3 main parts:
- Shaft
- Seal-plate assembly
- Mechanical stop
The steal-plate assembly travels up and down the shaft to open or close the passage. When the assembly makes it to the bottom of the passage, closing it off, the assembly connects with the mechanical stop, which holds the assembly in place and forms a seal. Like the poppet valve, the gate valve has up and down linearly and can be manual or pneumatic. The shape of the gate can either be round or rectangular.
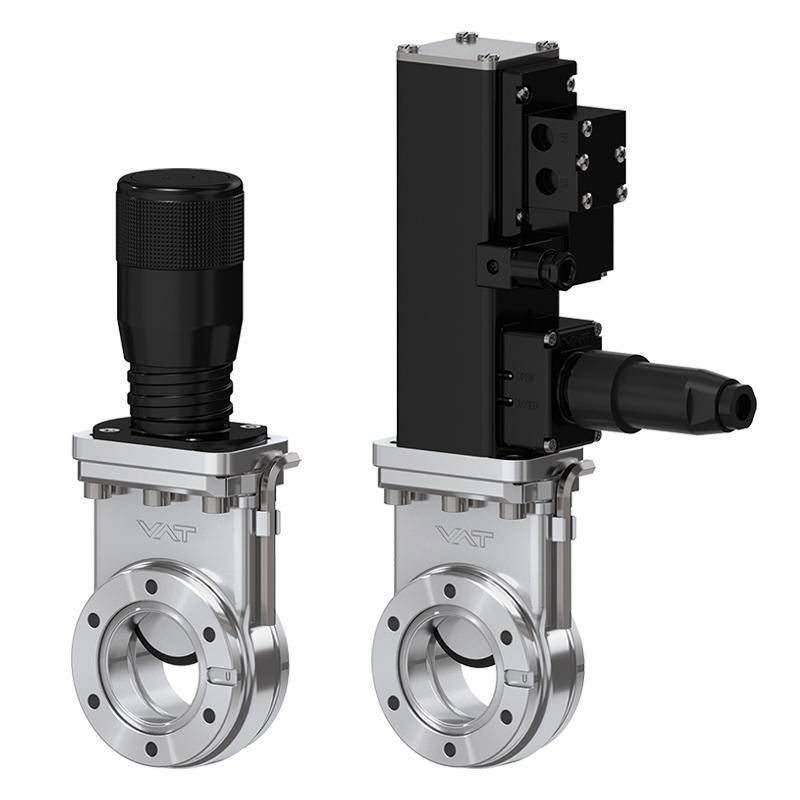
The main advantages to gate valves are:
- Material Strength
- Durability
- Ease of Maintenance
- Ultra-high vacuum (UHV) suitable
ANCORP sells VAT gate valves, which are made of high-quality aluminum. This which ensures joint integrity and eliminates the possibility of virtual leaks.
VAT gate valves also provide service for 50,000 cycles before having to be serviced in most applications. When service is required, the carriage is easily removable, as is the solenoid if used, and removing the valve from the system is not required.
Gate valves can also be used for ultra-high vacuum systems, which ball valves cannot. Gate valve applications include isolation between vacuum chamber and pump, isolation between the chamber and the load lock during sample introduction, access between the chamber and the load lock during sample transfer, and isolation between synchrotron beam lines and experimental stations.
Disadvantages
Vacuum gate valves do come with some disadvantages, including:
- Collection of byproducts
- Complicated internals
Like angle valves, gate valves also have the problem of collecting byproduct from the system on the sealing surface. This issue can be an inconvenience and can cost time and money getting people to clean the byproduct. Ball valves generally avoid this issue.
Gate valves also have the issue of complicated internals. This means that maintenance and repair can be more involved, and therefore, costly to the owner of the system.
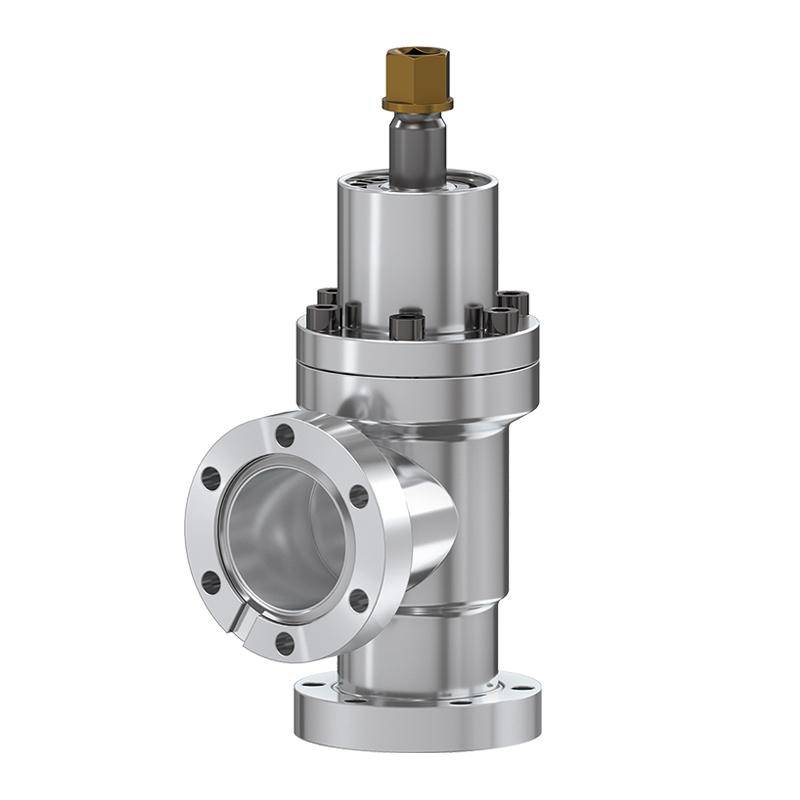
Overall
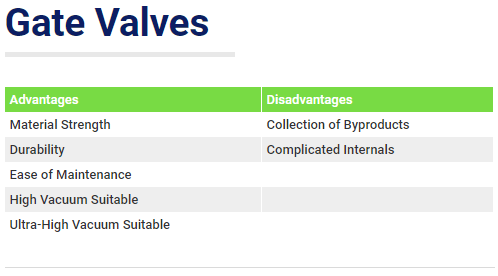